Lean manufacturing is a strategic approach to production that prioritizes efficiency and responsiveness. By streamlining processes and reducing waste, lean manufacturing aims to minimize lead times and enhance customer satisfaction.
The Roots of Lean
The concept of lean manufacturing was popularized by John Krafcik in 1988, drawing inspiration from the Toyota Production System (TPS). This revolutionary system, developed by Toyota in the post-war era, is built upon two core principles:
- Just-in-time (JIT) Inventory: By producing goods only when needed, JIT inventory minimizes waste and reduces storage costs.
- Automated Quality Control: Implementing rigorous quality control measures at every stage of production ensures product excellence and eliminates the need for costly rework.
The Lean Philosophy
Lean is founded on the concept of continuous and incremental improvements on product and process while eliminating redundant activities. “The value of adding activities are simply only those things the customer is willing to pay for, everything else is waste, and should be eliminated, simplified, reduced, or integrated.”
Lean is a continuous improvement approach that systematically identifies and eliminates waste to increase productivity, reduce costs, and minimize lead time, ultimately achieving optimal quality.
6s
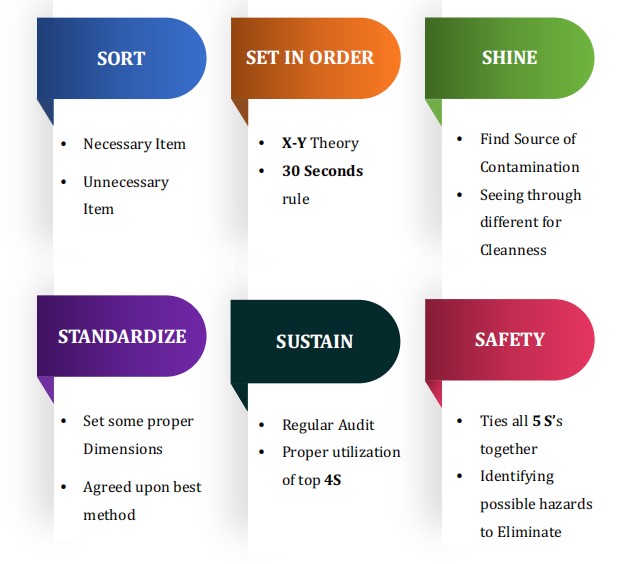
The 8 Wastes in Garment Manufacturing
In the garment manufacturing industry, eight types of waste, collectively known as TIMWOOD, can significantly impact efficiency and productivity. These wastes include:
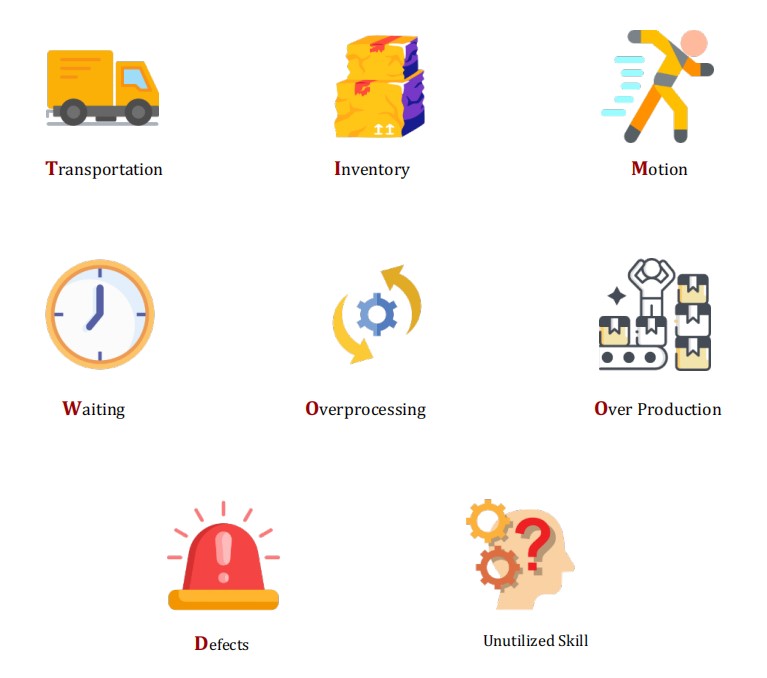
- Transportation: Inefficient movement of materials and products.
- Inventory: Excess stock of raw materials, work-in-progress, and finished goods.
- Motion: Unnecessary movement of people and equipment.
- Waiting: Idle time due to delays or bottlenecks.
- Overprocessing: Performing more work than is necessary.
- Overproduction: Producing more than is needed or demanded.
- Defects: Errors or mistakes in products or processes.
- Unutilized Skill: Not fully utilizing the skills and talents of employees.
This lean statement emphasizes the importance of creating a safe and healthy work environment in the garment sector. It outlines four key components of a comprehensive approach to safety and ergonomics:
- Proper Training: This involves educating employees about safety procedures, recognizing potential hazards, and using equipment safely.
- Ergonomic Design: This focuses on designing workstations and tools to fit the human body, reducing strain and preventing injuries.
- Personal Protective Equipment (PPE): This includes providing and ensuring the proper use of equipment like gloves, masks, and safety glasses to protect workers from hazards.
- Ongoing Monitoring: This involves regularly assessing the workplace for safety hazards, identifying areas for improvement, and implementing corrective actions.
Leave a Review